Cleaning heat-exchangers with the largest ultrasonic tank in the world
Updated: Jan 29
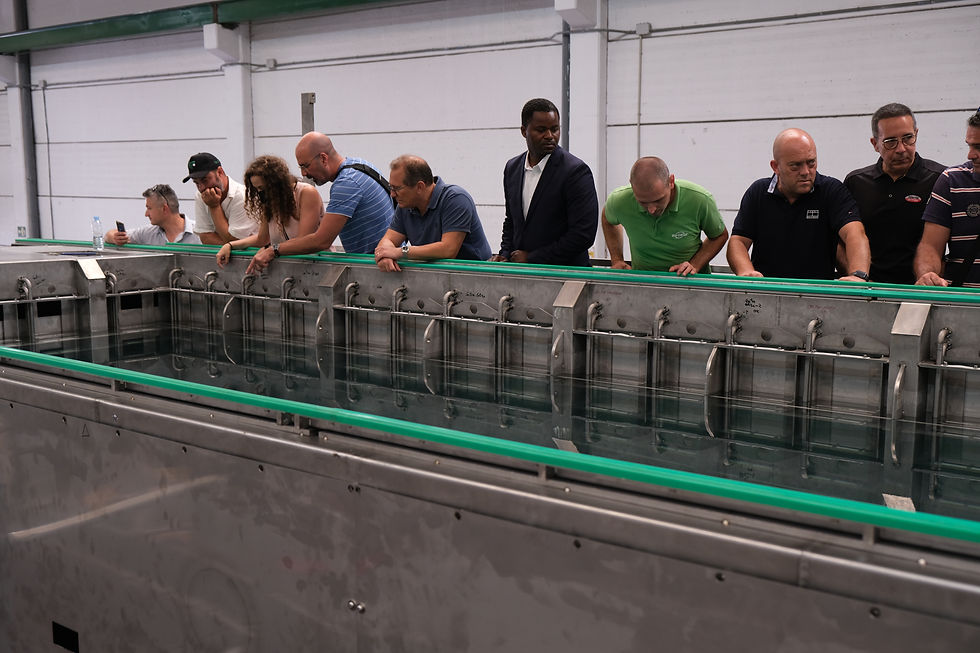
ULTRATECNO presented its latest creation for the OIL & GAS sector in an exceptional open day: the largest cavitation cleaning tank ever built and is ready to go around the world. Those who work in the industrial cleaning sector are familiar with the technology of ultrasonic tanks which exploits the effect of controlled cavitation to remove dirt from any object and of any size. With 50 years of experience, ULTRATECNO (UT), a Spanish company based in Valencia, knows the subject well and is, globally, one of the "top players" in this sector. We at MEDITERRANEAN INDUSTRIAL SERVICES, industrial cleaning technology consultants and UT partners were there and would like to share our impressions with you.
Record breaking size
The first impact with this tank is certainly its size - 57,000 liters. Built on a 40 'container platform, it is capable of handling tube bundles over 9m long. Commissioned by a Dutch contractor, specializing in chemical washing for heavy and non-heavy industry, it is destined to travel to all the refineries and petrochemicals of the world, from the cold climates of northern Europe to the arid deserts of the Middle East. The customer's goal is to offer a service that drastically reduces the time and costs of washing operations at the stops and, at the same time, improves the quality of the cleaning results compared to those obtained with traditional methods (eg hydroblasting).
Using the technology and its advantages

28Khz Technology
All the tanks built by UT are intended for "heavy duty" uses: 28kHz of (low) frequency which generate larger and more powerful cavitation bubbles; fixing of the piezoelectric transducers to the tank and patented synchronized wave management system for optimal cleaning efficiency; use of high quality materials; engineering and processing exclusively "in house".
The Challenge
Even applied on such a large scale, the performance is absolutely impressive. With the wise choice of the suitable detergent, this solution allows to remove in an effective, homogeneous way and in all parts, even those not visible, contaminants such as: rust; sludge; heavy oils; tar and asphalt; salt deposits (eg Calcium). All this takes place without the risk of damaging the most vulnerable parts of the bundle such as tubes and expansions or affecting the materials (steel; aluminum; copper; bronze, cast iron). According to UT's experience, this technology is able to bring back the clock hands of the heat-exchanger, in the sense that, unlike traditional methods, it allows to bring its efficiency up to 95% of the original one every time, thus lengthening the useful life of the product and preserving the project performance.
The Solution
Overall, beyond the size of the machine, cleaning equipment with ultrasound technology has advantages that far exceed the traditional ones to the benefit of both the Contractor and the Client. Worth mentioning are:
Less time for cleaning
Even and deep cleaning
Less water used (a tank can clean several heat-exchangers without requiring spare parts)
Less use of direct personnel and greater safety of operations
In a general stop, there are a lot of elements to clean besides the heat-exchangers, which is why our Dutch friends are not limited only to these. With such a tank we can clean elements such as: dishes and fillers of distillation columns; valves; impellers of pumps and compressors even turbine rotors.
This is why we at MEDITERRANEAN INDUSTRIAL SERVICES are committed to disseminating this technology among the operators in the sector because, we believe, it is one more step towards a more efficient and less costly way of working for the environment.

Comments